Quick Tech CNC: Simple Tools for Fast, Accurate Machining
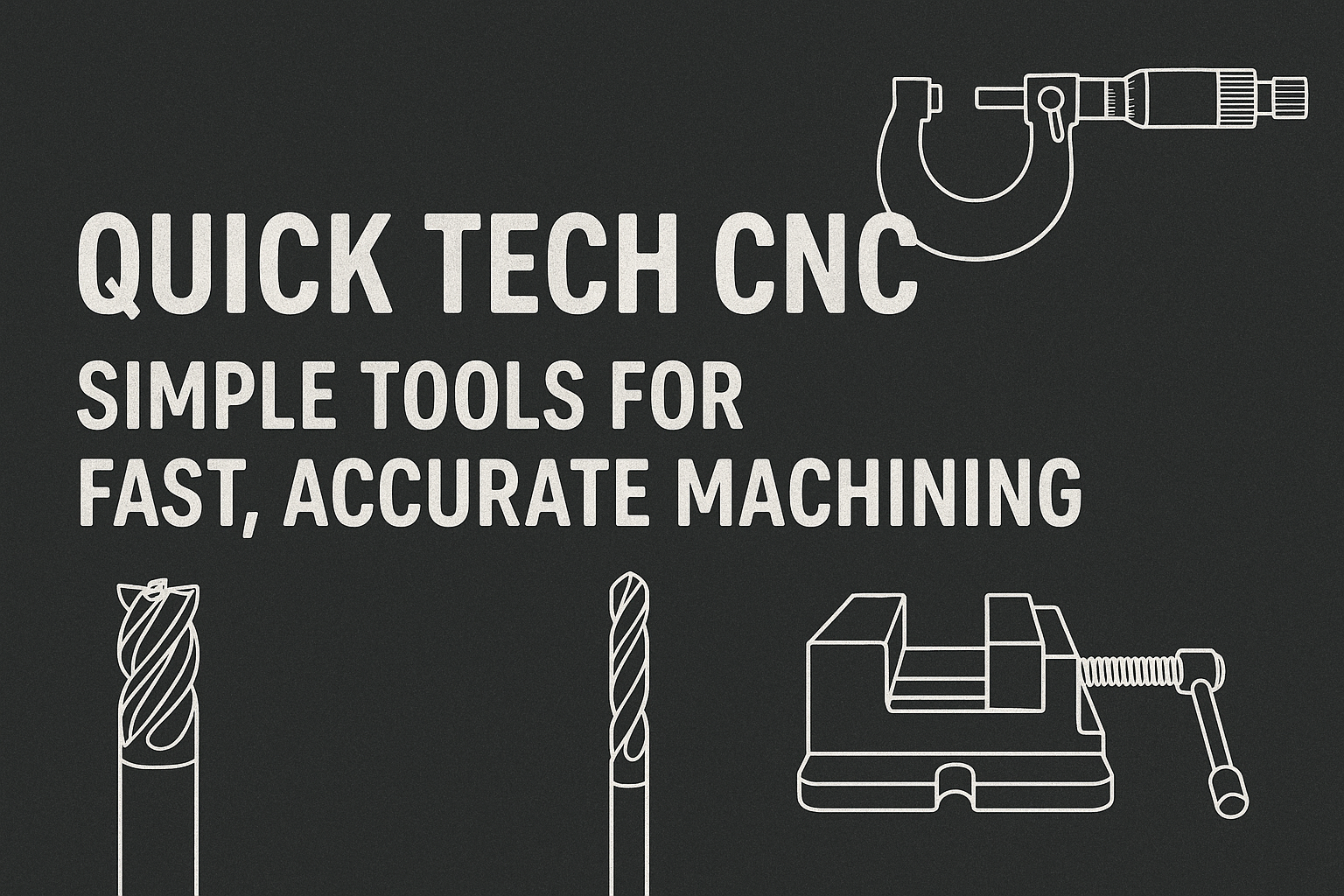
CNC machines are common in modern manufacturing. They cut materials with high precision. Quick Tech CNC makes these tools easier to use. It focuses on fast setup and simple operation. These machines work for small shops and hobbyists. They do not need big spaces or complex setups. Quick Tech CNC is compact and easy to run. Users can start projects quickly.
The brand offers lathes, mills, and engravers. These tools handle wood, metal, and plastic. Software is easy to learn. Projects go from idea to product faster. This post will explain how Quick Tech CNC works. We’ll look at its parts, uses, and benefits. You’ll also see how it compares to older machines.
What Is Quick Tech CNC?
Quick Tech CNC builds small, smart machines. These tools cut and shape materials with code. The code tells the machine what to do step by step. Each machine is built for speed and ease. Setup takes minutes, not hours. This helps users get started fast. There is less waiting and more making.
These tools work with common design software. You can draw a part and send it straight to the machine. No extra steps needed. Quick Tech CNC targets makers, students, and small shops. It gives them power without complexity. Anyone can learn to use it with basic training.
Why Use Quick Tech CNC?
Quick Tech CNC cuts time and cost. Big machines take up space and cost a lot. These tools are smaller and cheaper. They fit in tight spaces. They are easy to learn. Old machines need long training. These tools have simple controls. New users can start in a short time.
Maintenance is low. Fewer parts break. Cleaning and light checks keep it running. Less downtime means more work done. They work well for quick jobs. Prototypes, repairs, and custom parts all fit. Speed and accuracy matter. Quick Tech CNC delivers both.
Quick Tech CNC vs Traditional Machines
Traditional machines are strong but slow. Quick Tech CNC wins in speed and access. It’s perfect for small teams and new users. Old systems often use outdated software. Quick Tech CNC links with modern tools. Design files go straight to the machine. You don’t need a big shop to use these. A table and a power plug are enough. That makes them great for home workshops and classrooms.
Key Parts of a Quick Tech CNC Machine
Every machine has core parts. The base holds everything steady. The spindle spins the tool. Motors move the tool across the material. A control box runs the system. It reads code and moves parts. Wires connect each section. Safety covers protect users’ tools change based on the job. End mills cut flat areas. Drills make holes. Engraving bits add details. Software turns designs into code. You pick a tool, set the speed, and start. The machine does the rest.
How to Start Using Quick Tech CNC
Start by choosing the right model. Do you need a lathe or a mill? Pick one that fits your work type. Check size and power limits. Set up the machine on a stable surface. Plug it in. Install the software. Connect the machine to your computer. Learn the basics with sample projects. Try cutting a square in soft wood. Watch tutorials and read manuals. Once ready, try real jobs. Make parts, signs, or gifts. Keep learning as you go. Each project builds skill.
Who Uses Quick Tech CNC?
Schools use these machines to teach skills. Students learn design and machining. Hands-on lessons build real-world knowledge. Small shops make custom parts. Repair shops fix old items. Artists create detailed pieces. All benefit from fast, precise tools. Hobbyists enjoy personal projects. They make toys, tools, and decor. CNC adds new options to DIY.
Read more: Online School College: A New Way to Earn Your Degree
Makerspaces share tools among users. Quick Tech CNC fits here. It is safe and easy to share. Prototyping labs test ideas fast. Engineers and designers make samples. Quick Tech CNC speeds up testing. Home users build furniture and gadgets. Compact size fits home garages. Fun and useful at the same time.
Benefits of Quick Tech CNC in Business
Small firms save money with these tools. They avoid big machine costs. Jobs finish faster. More work gets done each day. Custom work becomes easier. Clients want unique parts. Quick Tech CNC handles small batches. No need for mass production. Repairs take less time. Replacement parts print quickly. Downtime drops. Customers get results faster. Designers test ideas before full runs. Mistakes are caught early. Costs stay low. Marketing improves with real samples. Clients see working models. Trust grows. Sales follow. Team members learn fast. Training is short. More people can help. Workloads are spread out.
How to Choose the Right Quick Tech CNC Model
Check your work type first. Need a lathe or mill? Decide based on the shapes you make. Lathes turn round parts. Mills cut flat ones. Size matters. How big is your workspace? Desktop models fit small tables. Larger units need more room. Power affects material choice. Soft metals and wood need less force. Hard metals may require stronger tools.
Budget sets limits. Prices vary by features. Add-ons like probes or extra tools cost more. Talk to sellers or users. Read reviews online. Ask about support and updates. Pick a reliable seller. Test a demo if possible. Run a sample job. See how it feels. Smooth movement and quiet noise mean quality.
Setting Up Your Quick Tech CNC Machine
Place the machine on a solid table. Avoid shaky surfaces. Vibration harms accuracy. Keep the area clean. Plug in the machine and the computer. Connect via USB or Bluetooth. Install drivers if needed. Mount the tool in the spindle. Use the correct size bit. Tighten it well. Loose tools cause errors. Load your design file. Set the origin point. Press start. Watch the first few seconds. Stop if something looks wrong.
Tips for Safe Operation
Wear eye protection always. Chips fly during cutting. Gloves may catch on moving parts. Skip gloves unless handling sharp edges. Keep your hands away from the tool. Let the machine work. Don’t reach in while running. Use dust collection. Wood and plastic make fine particles. Breathe safely. Clean air is key. Secure the material. Clap it tight. Loose pieces cause bad cuts. Double-check before starting. Turn off the machine when done. Unplug if storing. Clean chips and dust. Lubricate moving parts as needed.
Future Trends in Quick Tech CNC
More machines will link to cloud services. Users can send jobs remotely. Updates come through Wi-Fi. No need to install manually. AI will help with tool paths. It picks the best route for cutting. Less wear on tools. Faster jobs. New tools will combine functions. Some machines will cut, drill, and 3D print. One unit does more. Sensors will warn of issues. If something breaks, the machine stops. Safety improves. Schools will use more CNC tools. Kids learn digital design early. Quick Tech CNC supports STEM goals. Prices may drop further. As tech improves, costs fall. More people can afford these tools.
Conclusion: Quick Tech CNC for Everyone
Quick Tech CNC brings advanced tools to more people. It is fast, simple, and affordable. Hobbyists, schools, and small shops all gain from it. Setup is easy. Learning is quick. Maintenance is low. These points make it ideal for many users. The future holds even better tools. Cloud links, AI help, and smart sensors will arrive. These upgrades will make the tools smarter and safer. If you want a CNC machine, Quick Tech CNC is a good start. It meets modern needs without big costs.
Read more: Best Wells Fargo Cash Back Credit Cards (2025 Guide)
Frequently Asked Questions (FAQ)
Q: Can I use Quick Tech CNC at home?
Yes. These machines are small and quiet. They fit in homes and garages.
Q: What materials can I cut?
Wood, plastic, aluminum, brass, and some steel types. Always check machine specs.
Q: Do I need special software?
Most models work with free or common CAD/CAM tools. Fusion 360 and Easel are popular.
Q: Are they hard to learn?
No. Basic training is enough. Many guides and videos exist for beginners.
Q: How much do they cost?
From $1,500 to $10,000 depending on size and features.
Q: Can I run them in a school?
Yes. Many schools use them for teaching design and engineering.
Q: Do they need regular maintenance?
Yes, but it’s simple. Clean, lubricate, and check tools once in a while.
Q: Can I make money with them?
Yes. People sell signs, parts, and custom goods made with these machines.
Q: How loud are they?
Loud but not unbearable. Ear protection is recommended.
Q: Where can I buy one?
Through official dealers, online stores, or directly from the maker.